Shipping solar modules can be expensive for a lot of reasons. The following are key contributing factors: the need to protect the solar modules in shipping, preventing them from being damaged and having glass shatter during transit; packing them with pallets better than just stacking them on top of each other and keeping them safe; and because they take up so much room, it’s difficult to load multiple packages onto one truck without paying more. All these things make shipping solar modules incredibly expensive!
Challenge For The Solar Industry
Shipping solar modules is a costly endeavor that can be expensive for many reasons. Here we will explore some contributing factors and what you should do about it!
The first factor is to protect them in shipping, because if these important items are damaged or their glass shatters on transit they won’t work properly and this will increase both your costs as well as installation time; wooden pallets provide better protection than plastic ones when loading onto trucks so make sure yours has plenty of cushioning around each panel The next point concerns how extensive packaging needs to be with such delicate products like panels… once loaded into an overcrowded truck space there’s no room left over – which means higher rates at peak times due simply too demand from suppliers wanting delivery of their own products!
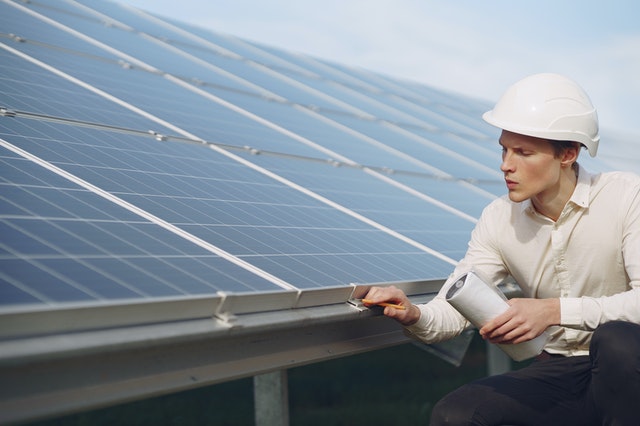
Another reason for high shipping costs is the damage during transport. The most dismaying situation, which happens all too often in our industry and can be avoided by proper handling of packages from start to finish with care taken at every stage-whether loading onto a ship or trucking them around countrywide, having said this there are always unforeseen circumstances beyond anyone’s control that drive up expenses like cracked solar modules due to rough handling.
Solar modules are delicate and need special care when transported. They should be well protected during shipping, which will allow them to reach their destination without any damages or harm done in transit.
(1) Some microcracks don’t always show up visually; however once these cracks become larger they could cause operational issues with your system down the line.
(2) It’ll lower energy output over time too so it’s best not let anything happen that may reduce efficient use of resources like this!
Solution For The Solar Module Microcracks Shipping Damage
Since the shipping damage leads to considerable loss for the solar industry, our priority for them is to lower the damage rate. Hence, the best solution for us is Shock indicator. The impact indicators help us solve the problems in two crucial ways.
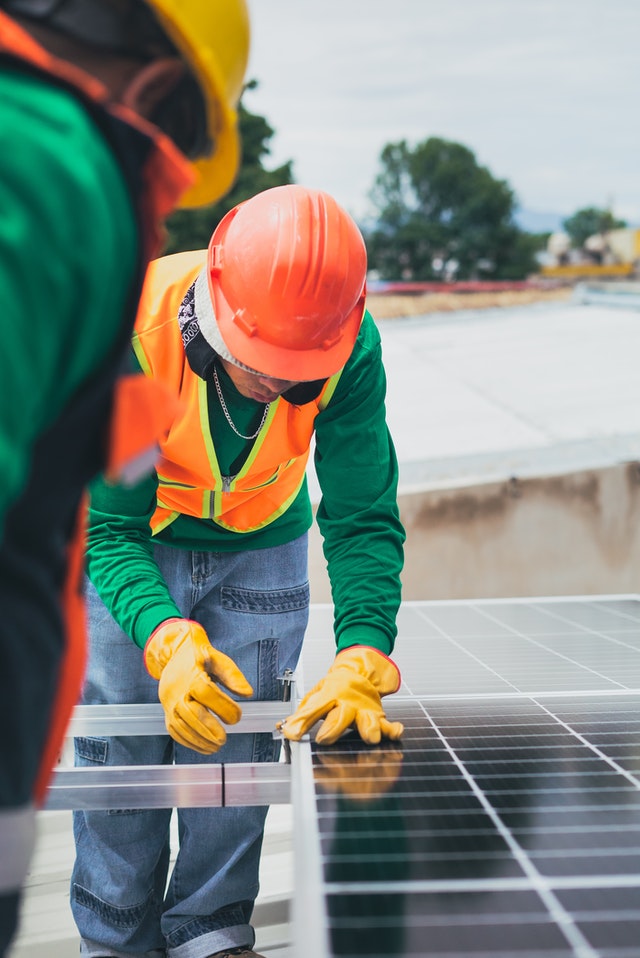
(1) Spot The Issue
With Shock indicator, our receivers don’t need to open the box to identify damaged goods. What’s better, the manufacturers don’t need to worry that the microcracks will have a negative impact on the operation system in the future. Because the g-force indicator label could effectively tell us when and where the boxes were mishandled. Tracking down the trouble spots is even easier so that we could effectively and efficiently assign accountability for our supply chain.
(2) Prevent Mishandling
With the impact indicator affixed to all the packaging, handlers know they must take extra caution when handling our cargo. The device is tamperproof, which means once it’s activated, no one could reset it or pretend impact never occurred. The impact indicator is not only a reminder for receivers, but for handlers.
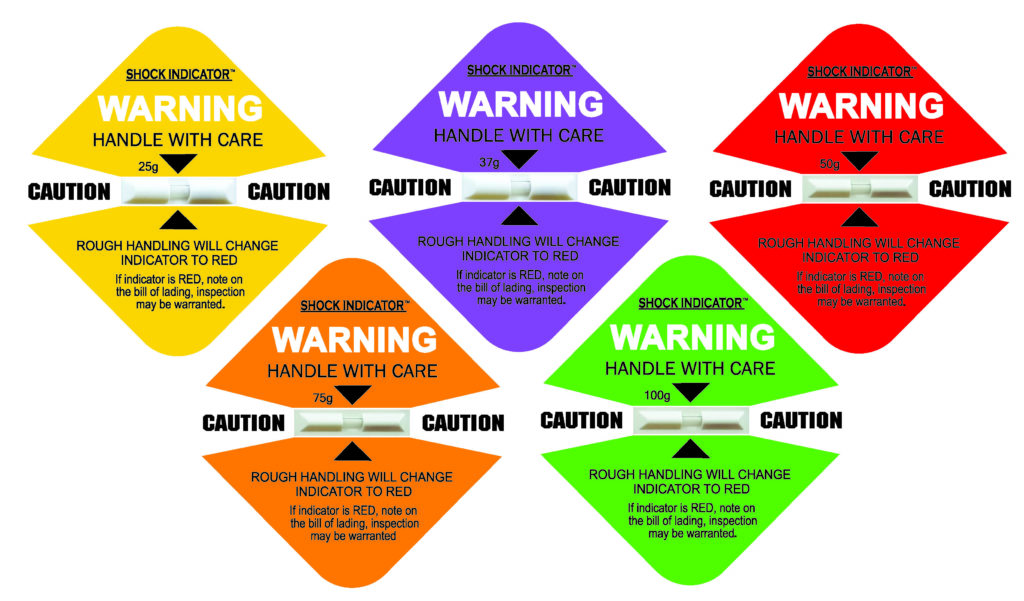
Benefits Of Applying G-Force Indicator Labels
After using indicators to monitor shipment of solar modules, we noticed that the damage rate has decreased over weeks. This allowed us to manage cost and improve our supply chain processes all at once!
Conclusion
If you want to eliminate the risk of shipping solar modules that are damaged, we recommend Shock indicator. We’ve noticed an improvement in our shipment’s damage rates as soon as we affixed their Shock indicator to all our boxes and packages. To learn more about how this can help your company, reach out today!