What happens when 66% of your medical equipment arrives damaged? You end up with a lot of lost money.
The package consisted mostly of medical instruments and devices that were being shipped from China, but it wasn’t handled properly in transit so many items were ruined or broken upon arrival at its destination. It’s unclear how much the damages amounted to, but this is an example of what can happen if you don’t take care during transportation!
It’s Critical To Ship Medical Equipment Correctly
For medical equipment producers, hospitals and others in the business of transporting assets there is always a risk that they may arrive damaged or not at all. This puts patients’ lives at stake because no matter what happens with an asset it cannot be used once its arrival has been delayed too long so you must go above-and-beyond to ensure everything arrives perfectly preserved from beginning till end every time!
Medical Equipment Shipping: Concealed Damage Causes 1 Million Dollars
In 2018, a prominent medical equipment manufacturer finished orders for 12 X-ray machines and cheerfully shipped them to clients. Customers were dissatisfied with the products they received; 7 of them have obvious scratches or malfunctions while one is exhibiting an abnormal pattern that could not be explained by its operator manual.
The loss was up $1 million dollars as customers lost faith in our company’s quality control measures which caused 66% damage caused delivery delays due poor reputation management strategy from senior executives . Senior managers then summoned supervisors from production ,shipping & purchase departments who had been assigned this task just weeks ago at their meeting three days prior where it became known what happened when inspecting first scores of equipment shipped.
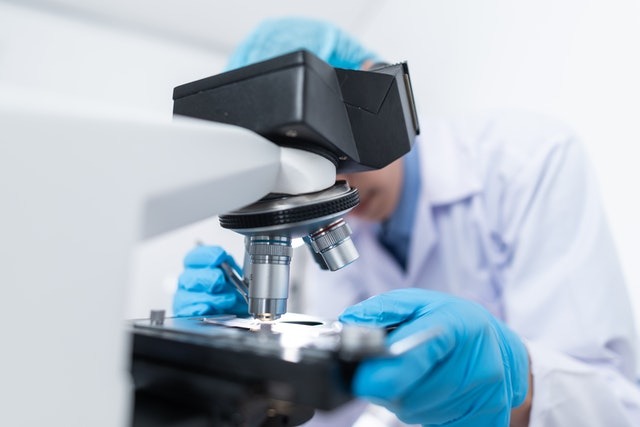
What Damages Medical Equipment
The container arrived at its port of destination wreaking havoc on other containers during shipping process; however the magnitude or damages cannot be determined due to lack of information about what happened when these boxes collided with each other while shifting around inside a dock – but we do know it was significant enough for them not only get damaged themselves but also cause damage which led up this whole investigation into our client’s equipment being mislabeled after delivery!
Equipment damage is very common, but the packaging has flaws that make it easier for equipment to get damaged.
- Packaging should be kept in wooden boxes with extra protection around edges and corners; this prevents hitches like what happened here when one box got pushed on top of another while shipping them out.
- Report any external issues as soon as possible so they can take care of fixing or replacing whatever needs mending!
- When containers are used instead–they don’t always line up perfectly next to each other due lack between boards which leaves gaps where items can move around and get damaged.
How Do I Pack Medical Supplies Safely And Securely
Whether to use bespoke blocking and bracing for the job, or just delegate this important task outsource has been debated by many companies over time. It might seem like less work but at what cost? Custom packaging will not only protect expensive items from damage during transit; they also ensure maximum safety with proper stabilizer bars inside every crate/corrugated cardboard box which is lined using bubble wrap around all sides except top – creating an outer layer that totally absorbs impact if something does happen along its journey!
When you invest in a reusable custom container, not only can it help protect your assets during transit but also save money. Link locks and hasps are easy ways to ensure that these containers shut securely without the need for tools- just attach them! You could even apply labels or stencils identifying yourself as an owner so there’s no confusion who owns what’s inside at all times too.
Medical supplies and equipment can be quite costly. As a result, it’s critical to insure them correctly and commit them to a logistics company that can trace them from collection to delivery.
How To Track Medical Equipment Packaging
Normal delivery is a complicated task. You have to make sure that your products get from point A to B without any damage, but proving liability for hidden flaws can be difficult when most recipients will just sign the certificate and not open up their package in typical circumstances. Luckily there are indicators on boxes which raise awareness of possible problems such as “Handle With Care” labels or even thicker packaging material at key points during shipping process – these help protect against potential losses caused by shippers carelessness towards customers’ goods!
Shockwatch: Change color when a box is dropped from a specific height or struck with a damaging amount of force from any direction.
Tiltwatch: When the container is tilted over 80 degrees, the label will change color.
According to data, using Shock indicator can reduce the loss of goods during transportation by 40-60%.
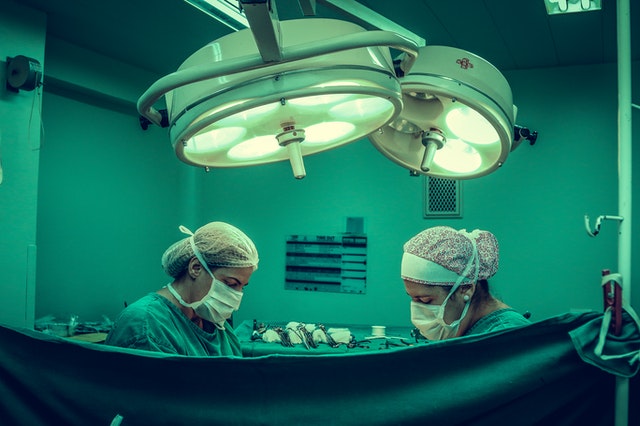
Conclusion
Medical equipment producers, hospitals and others in the business of transporting assets should be aware that damage can happen with any shipment. It is important to have an asset protection plan including insurance for your medical equipment so you are prepared when something goes wrong. If you want help, contact us today! We offer a range of services related to shipping damaged or non-shippable goods and we’re happy to work with customers around the world who need our expertise.